We showcase Hexagon’s partnership with ARCH Motorcycle to craft bespoke, high-performance cruisers, supporting the quality control demands of engineering and producing unique riding experiences.
BIKE TO THE FUTURE
ARCH Motorcycle (ARCH) owners seek more than just a machine.
Rather, these passionate individuals are in search of a completely immersive riding experience.
As such, each ARCH motorcycle is built from an obsession with innovative design, engineering excellence, and dedication to the rider.
Founded by Keanu Reeves and Gard Hollinger in 2011 to challenge the perception of what an American motorcycle could be, ARCH has partnered with Hexagon, a global leader in digital reality solutions headquartered in Stockholm, Sweden.
Hexagon is a major player in the industrial technology space, focusing on harnessing high-precision data to boost efficiency, productivity, quality, and safety across a wide range of industries including aerospace, automotive, construction, and mining.
The company’s cutting-edge technologies utilise data from design and engineering, production, and metrology to make manufacturing smarter, contributing to the production of 90 percent of aircraft, 75 percent of smartphones, and 95 percent of every automobile worldwide.
Whilst a lot of its business is centred around mass production, Hexagon’s measurement technologies are also trusted by precision manufacturers, including prominent names such as Hendrick Motorsports, Oracle Red Bull Racing, and the regulatory bodies of F1 and WorldSBK.
By taking advantage of the technologies behind industry giants, smaller manufacturers can enhance their accuracy, quality, speed, and cost-effectiveness without compromising on creativity, allowing them to push the boundaries of what is possible in bespoke motorcycle manufacturing.
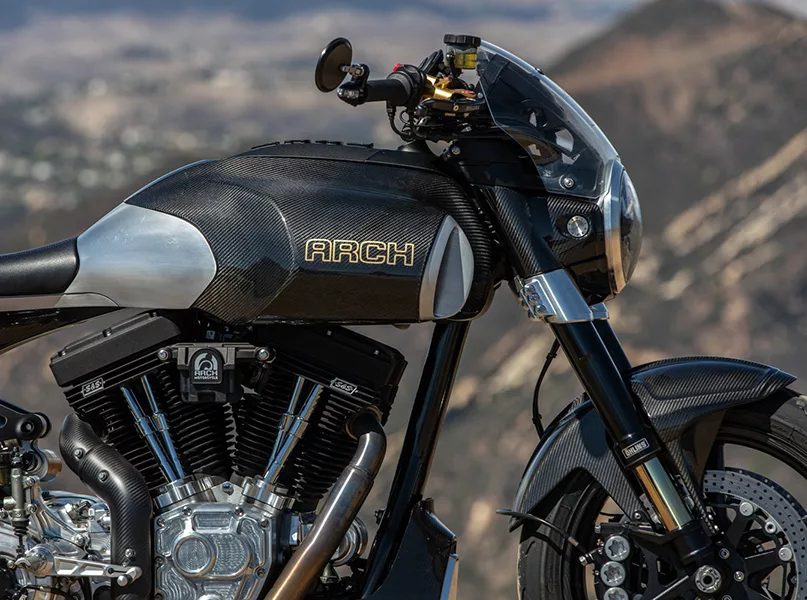
HARNESSING DIGITALISATION
The Hexagon partnership is all about harnessing the power of digitalisation to elevate quality and efficiency.
Indeed, it is geared to help ARCH expand its commitment to producing bespoke motorcycles by fully digitising quality processes throughout engineering and manufacturing with advanced measurement technologies.
Hexagon technologies to be implemented by the ARCH manufacturing team include an easy-to-use portable measurement arm and a state-of-the-art 3D laser scanner.
The latter provides a guided workflow that helps users visualise 3D models and, paired with tightly integrated measurement software, simplifies the scanning of large components and reverse engineering of parts.
Hexagon’s 3D laser scanning technology therefore helps companies such as ARCH to capitalise on time invested in previous projects by providing the ability to retain, reuse, and apply elements of successful designs for products in development.
As a result, there is no need to return to the drawing board for time-consuming development when existing design data can easily inform and enhance in-progress designs.
3D laser scanning also makes it possible to easily capture accurate measurement data to ensure that high-quality parts are being accurately produced and can be seamlessly assembled.
Hexagon’s laser scanning solutions help ARCH to create tailored, ergonomic motorcycle designs that incorporate individual customer specifications. By digitising these customisations, they can be seamlessly integrated into the manufacturing process.
This blend of craftsmanship and digital efficiency strengthens ARCH’s ability to produce meticulously finished bikes while maintaining repeatability and precision.
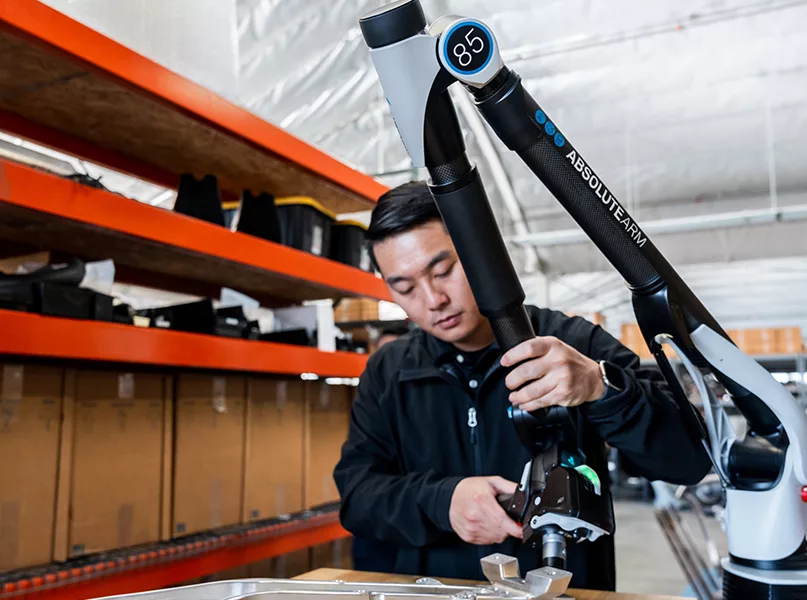
DIGITAL BLUEPRINT
Highly custom manufacturing entails keeping track of a much larger number of details and differences that may appear minor but could significantly affect the success of a project.
However, the partnership with Hexagon allows ARCH to keep an accurate digital 3D record of each customer’s motorcycle, supporting future customer service and potential customisations.
Keeping a paper trail of job details and changes is a comparatively error-prone and time-consuming endeavour that diminishes throughput and makes it difficult to communicate project details across departments and teams.
Fully digitised processes, on the other hand, provide a blueprint that everyone can easily follow, from engineers through to production and inspection personnel.
This ensures that staff have access to identical, up-to-date, accurate, and easy-to-access information, streamlining communication and reducing errors.
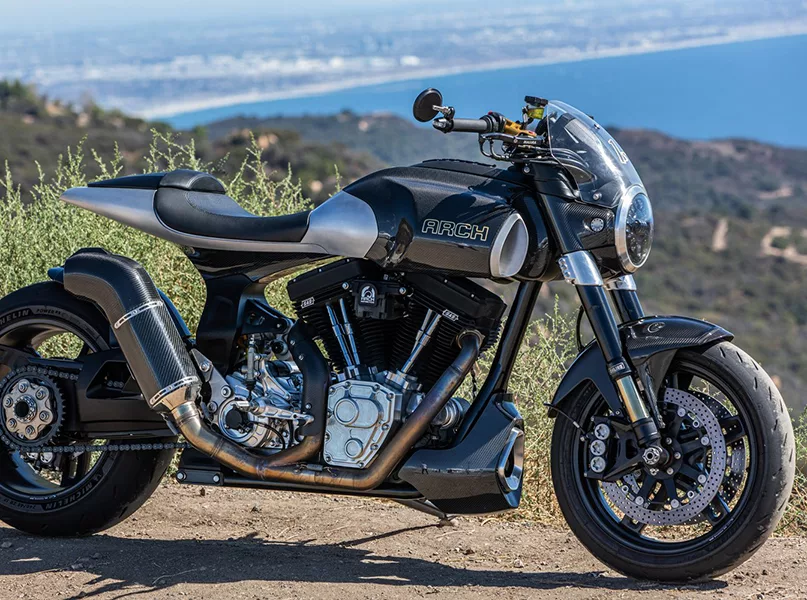
Hexagon has therefore found a natural partner in ARCH and understands the unique passion and appeal of its bikes.
This collaboration is a starting point that extends beyond digitising parts; it’s about enhancing future product development workflows.
Now that ARCH has the ability to quickly digitise parts, it is also streamlining its 3D digital workflows for computer-aided design (CAD), making 3D scanning an invaluable part of its future product development.
The partnership is a great example of the benefits of combining precision engineering with cutting-edge technology that has been tested and proven at production scale.
Together, Hexagon’s metrology expertise and ARCH’s artistry demonstrate a shared commitment to excellence in craftsmanship and innovation.