INTRODUCTION
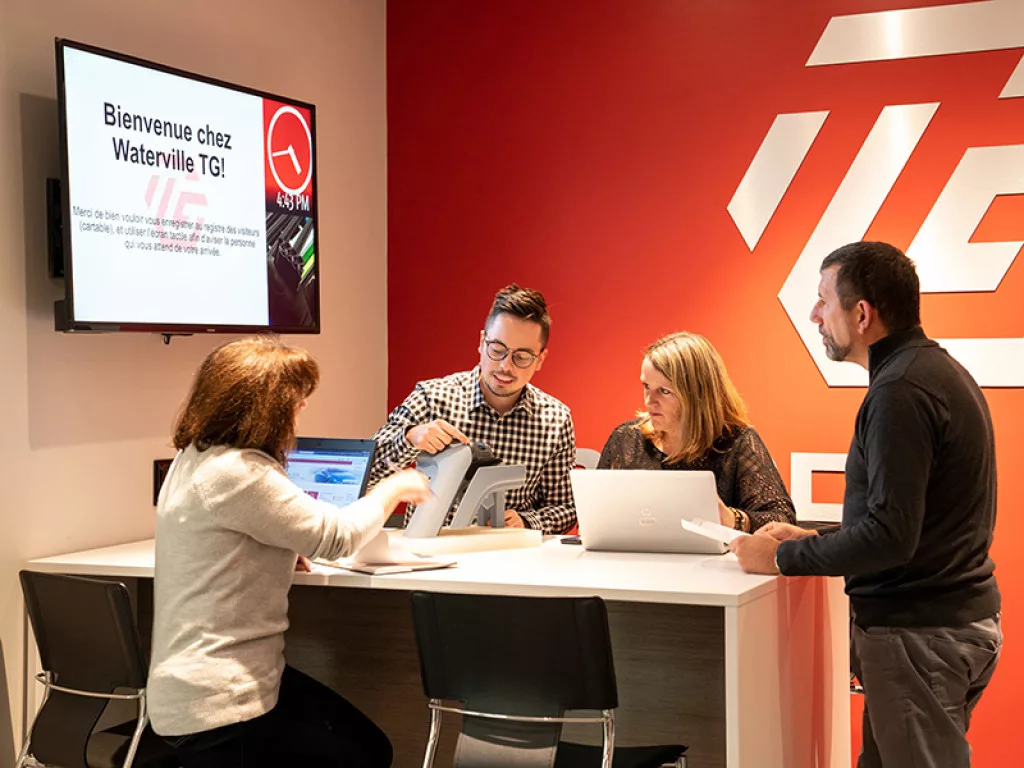
SEALING SPECIALIST
Indeed, the company has been recognized internationally as a convertible vehicle sealing specialist, with the quality and reliability of Waterville’s products setting it apart from the competition.
“We have the capability to develop the full product, from design to day-to-day support and delivery, and a very strong program development team that supports our customers through the complete lifecycle of their vehicles,” Tetreault says.
“Furthermore, we have an experienced material development team that can quickly develop new formulations, ensure compatibility between various materials, and our chemists ensure the support of our sister companies as well.”
Waterville’s engineering team is just as integral to the organization, specializing in various fields of expertise from artificial intelligence (AI) and robotics to manufacturing and engineering.
“This team is leading the way towards global competitiveness and developing new technologies,” adds Tetreault.
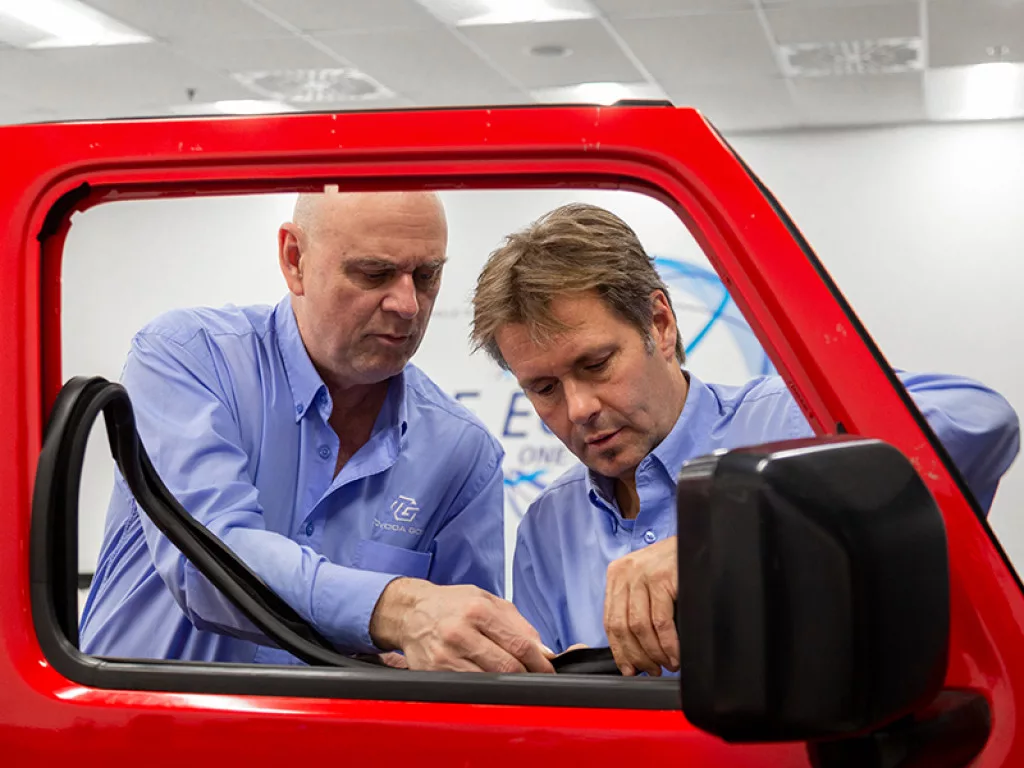
POSITIVE IMPACT
As an active member of the community, being a good corporate citizen is a priority for Waterville.
“For us, social responsibility is about the positive impact our company can have on preserving the environment, creating pleasant workspaces, and helping to build communities that people want to live in,” Tetreault emphasizes.
“Our company contributes to the local economy by providing quality and stable jobs for hundreds of families locally. We also partner with local engineering firms, develop new suppliers, and purchase tools and components from local vendors.”
Waterville’s commitments to the community include support for organizations such as Centraide Estrie (United Way), taking part in the non-profit’s awareness campaign every year.
Many employees also make donations to Centraide Estrie through automatic payroll deductions, with special prizes given out to donors by Waterville to encourage employee participation.
Elsewhere, the company makes financial and material donations to the likes of Blue Massawippi and FSWC Québec, and supports a variety of projects in the city of Waterville.
“We also like to encourage university students by supporting their engineering projects and competitions, as well as sports organizations.”
Equally, Waterville’s Better Health program is centered on wellness and allows staff members to enjoy a fulfilling lifestyle.
Better Health focuses on physical and mental wellbeing in five specific areas: Eat Better, Breathe Better, Be Safer, Live Better, and Move Better.
“We try to implement different types of activities so that the program appeals to everyone,” Tetreault shares.
“For example, we have a massage therapist that comes to the Waterville plant every week, we have several gym and spa discounts, and we hand out fresh apples in the fall.”
REDUCING WASTE
To minimize its environmental footprint, and eliminate the landfilling of production waste, Waterville has recycled waste weatherstrip rubber processed outside the factory for almost 20 years.
“We have surrounded ourselves with processors, and brought our technical expertise with rubber into the equation to allow a significant reduction of material going to waste,” outlines Tetreault.
More recently, the company was awarded the Eastern Townships environmental excellence prize and is now recycling 70 percent of its residual materials.
Waterville is also constantly optimizing its coating systems to reduce landfilled waste, lowering the amount of silicone used and alleviating volatile organic compound (VOC) emissions.
Numerous recycling projects, meanwhile, have been implemented to prevent other materials from going to landfill, including paper, cardboard, glass, metal, wood, and plastic.
“We also promote composting, and in our recycling business relationships, we prefer local businesses in order to reduce our carbon footprint to the maximum,” Tetreault notes.
Another of Waterville’s environmental goals is to increase the reuse of reclaimed EPDM rubber in compound mixing, based on a new ‘cradle-to-cradle’ mantra.
This year, the company will be pursuing an R&D project with the intent of increasing the ratio of reclaimed material inside new batches of rubber.
“The end goal is to revalorize products by reintroducing them into the production process. One of the challenges is the reclaiming process itself, to design the product with reuse in mind and the collection of material following its usage.”
Waterville has a track record of environmental leadership, having been a member of the Canadian Industry Program for Energy Conservation (CIPEC) since 2004.
CIPEC recommends best practices in energy management, and encourages reductions in the consumption of energy per unit of production whilst improving economic return. Waterville has subsequently had an electricity management system (EMS) in place since 2014, enabling the implementation of systematic energy management.
The company has also been involved on the Board of Directors of the Fondation Estrienne en Environnement (FEE) since 2007, promoting environmental protection and sustainable development in the Eastern Townships region.
As a FEE member, Waterville has now participated in expert networks and drafted guidelines dealing with the adoption of best practices in the industry for several years.
“Waterville participates in the sharing of knowledge, with the goal of having a positive impact on the industry,” Tetreault states.
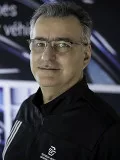
“We are a supplier of dynamic and static weatherstrip systems for the automotive industry”
Benoit Tetreault, President, Waterville TG
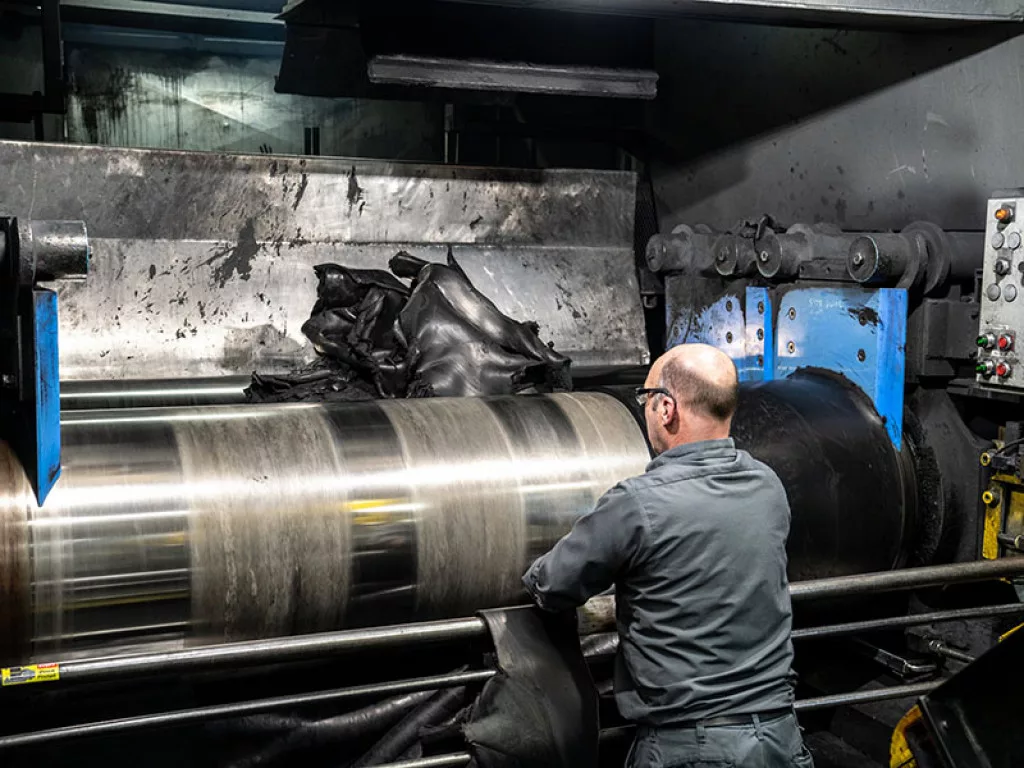