Long cycle life, high energy density, and resistance to shock and vibration are common requirements in AGVs and other types of mobile robot – How do they affect the choice of chemistry, cell, and battery pack design?
Efficiency, maximisation of throughput, safety, and operating cost reduction are the watchwords of today’s smart, digitalised factories and warehouses. To meet these business objectives, industrial companies are automating more processes and deploying more robotic devices, particularly various types of mobile robots. These include devices such as automated guided vehicles (AGVs) used in materials handling and other applications, automated mobile robots (AMRs) for last-mile deliveries, and frame climbers in automated warehouses.
One of the advantages of mobile robots in comparison to their human counterparts is the ability to continue working 24 hours a day without the need for breaks. However, this calls for a portable battery power system that can maintain a continuous output without running out of charge or failing prematurely because of a fault or breakdown.
This highlights the importance of specifying a mobile robot’s battery pack the right way. In nearly all cases, a mobile robot will require a custom battery pack to meet the application’s requirements for capacity, size, durability and ruggedness, peak power output, cycle life, temperature tolerance, and other factors. This means that choosing the right custom battery pack manufacturer is also a critical decision.
Lithium-based batteries have become the most common choice for new industrial batteries today because of their high energy density and capacity, giving much longer run-time between charges than any other battery chemistry. In fact, many types of lithium formulations may be used in battery cells, and the technology and production of these cells and packs are constantly advancing, giving original equipment manufacturers (OEMs) the benefit of improved specifications year-on-year.
So, what is the latest best practice for battery pack specification, and what are the key considerations that mobile robot OEMs should be taking into account today when specifying the cell type, pack design, and quality criteria?
SPECIFYING A BATTERY PACK: BALANCING THE TECHNICAL TRADE-OFFS
The proliferation of lithium chemistries and the components, such as battery charge controller ICs that support lithium battery packs, mean that a robot OEM can be faced with a complex set of trade-offs to consider. Cell chemistries such as lithium nickel manganese cobalt oxide (NMC), lithium iron phosphate (LFP), lithium titanate (LTO), lithium manganese oxide (LMO), and lithium cobalt oxide (LCO) vary on a range of parameters:
- Energy density, affecting the size and weight of the battery pack
- Maximum peak power output
- Maximum safe operating temperature and susceptibility to thermal runaway
- Cycle life
- Nominal output voltage
- Maximum charge rate
The decision about the best set of trade-offs needs to be made on an application-by-application basis. For instance, in a small AGV or AMR carrying light loads, the battery pack will typically make up a substantial proportion of the robot’s total weight and take up a large space relative to its enclosure. Here, high energy density is a key requirement to produce the smallest and lightest possible battery, a requirement that would generally call for the use of NMC cells.
On the other hand, in a large mobile lifting platform capable of shifting loads of as much as 1,000 kilogrammes (kg), the battery pack will make a negligible contribution to total size and weight. Here, energy density is of little importance, so the platform OEM could instead choose LFP cells; their energy density is at least one-third less than that of NMC, but their cycle life is much longer – more than 2,000 cycles, compared to as few as 500 to 600 cycles in some NMC implementations. LFP cells also operate safely at much higher temperatures than NMC, easing the design requirement for thermal dissipation, thermal monitoring, and safety circuitry.
Cycle life and charge time are crucial parameters for many mobile robots. AGVs in a smart warehouse, for instance, might work 24/7 all year round. A typical configuration uses a removable battery pack, allowing the AGV to return to a charging point for the removal of a discharged pack and its replacement by a newly charged pack. In this case, packs are continually cycling through the charge/discharge process. Therefore, the cells in the pack need to be able to withstand many charge cycles and fast charging so that they are available for use quickly after removal from an AGV in a discharged state.
A reputable battery pack manufacturer will be able to provide detailed guidance about these and every other performance attribute of each lithium chemistry and advise on the best choice for the OEM’s mobile robot application.
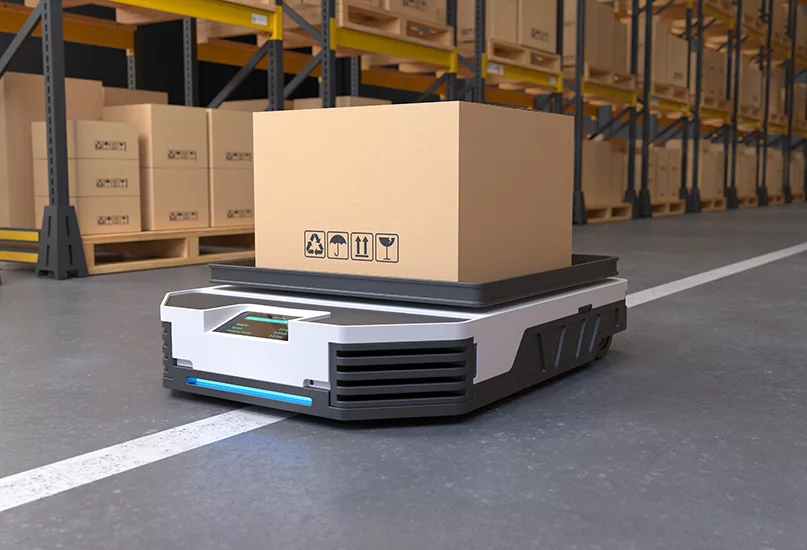
FEATURES AND APPROVALS: GETTING THE BATTERY PACK SPECIFICATION RIGHT
The choice of chemistry is just the start of the process of procuring the right battery pack for a mobile robot.
The evaluation of a custom battery pack manufacturer will normally be centred on the questions of features and quality.
The pack manufacturer should support the robot OEM’s application with the appropriate set of capabilities and features. These could include:
- Thermal management features – As they discharge, batteries generate waste heat, which needs to be dissipated to keep the pack at a safe operating temperature. Sophisticated designs use innovative cell array configurations to draw heat out efficiently, reducing or eliminating the need for a heat sink. This saves space, weight, and cost.
Equally, mobile robots that operate in a cold environment, such as a refrigerated warehouse, need to take into account the battery temperature, as a lithium cell cannot normally be charged when it is colder than 0°C. This might require the use of active in-pack heating technology to raise the cell temperature above 0°C in preparation for charging. In many applications, active heating is a better solution than depositing the pack in a space at room temperature and waiting for it to draw heat from the ambient air. - Telematics – A factory operator can exercise control of a fleet of AGVs or other mobile robots more effectively if it has access to data about each battery pack’s state of charge and health. Advanced custom battery packs can include wireless connectivity, such as a Bluetooth® Low Energy radio, configured to provide real-time data about charge status, battery temperature, and other key parameters.
- Regulatory compliance and approvals – The regulatory framework in which a battery design is made will depend on the countries or regions in which the pack is intended to be used. Regulation is a fast-moving field in which the battery pack manufacturer should be able to provide up-to-date advice. For instance, changes to US regulations have tightened the compliance requirements for cells and battery packs in mobile robots such as AGVs, bringing them into line with the regulations applying to battery electric vehicles (BEVs). A custom battery pack manufacturer’s design should provide a smooth path through testing, approval, and certification for any part of the world in which the robot OEM intends to market its products.
QUALITY AND RELIABILITY: HOW TO EVALUATE THE PRODUCTION PROCESS
After specifying the cell chemistry and the right set of features, the battery pack manufacturer will generate a pack design. When the testing and approval of final prototypes have been completed, the pack will go into production. At this point, the OEM is at the mercy of the manufacturer – there is no second source for a custom battery pack.
So how is an OEM to assure itself of the quality of the battery pack that it has specified?
In battery pack manufacturing, quality is not a bolted-on feature or a control process applied at the end of the production line; if quality is not built into the entire process from the start of its design, there will be shortcomings in the production units coming off the line.
Attention to quality starts with the choice of lithium cell. The world’s three largest manufacturers – Samsung, LG, and E-One Moli Energy – test all cells for adherence with all relevant safety and compliance requirements. There is a unit cost premium to pay for the quality and safety of the best cells compared to those from unbranded cell manufacturers, but this up-front cost is more than recovered in the longer lifetime and superior safety assurance of the more expensive cells.
Alexander Battery Technologies (ABT) has secure supply arrangements with the three premier cell manufacturers, exclusively utilising cells from these companies.
The application of quality principles should also be evident throughout the production process. In assembly, high-quality pack manufacturers will pay particular attention to the elements of the structure that are most prone to failure, such as welds. For instance, advanced optical inspection techniques should guarantee that welds exceed high minimum thresholds for size and integrity, ensuring that the pack’s electrical connections remain sound even when exposed to the extremes of shock or vibration specified in the application.
Some manufacturers will follow the practice that ABT has instituted of inviting customers to inspect its manufacturing facilities in detail. Modern enterprise resource planning (ERP) software systems may also be used to enable the customer to perform unit-by-unit monitoring and inspection of the production output of their packs.
High-quality design and production also support the rapid, first-time-right validation and certification of battery packs according to the high standards set in sectors such as the automotive industry.
BATTERY PACK PRODUCTION FOR A NEW ERA OF MOBILE ROBITICS
The advance of digitalised and smart manufacturing and warehousing practices is leading to a rapid increase in the number and variety of mobile robots deployed in industrial settings. Operators rely on these robots to maintain unbroken operations 24/7; unforeseen downtime severely impairs throughput and efficiency.
The battery power supply can be as reliable as any other component of a mobile robot. The guidance above shows how careful attention to cell and battery specification, design, production, and the choice of a dependable pack manufacturer can ensure reliable and predictable performance for the life of the robot.