TOWING AND RECOVERY TITANS
Following the completion of distributor consolidation in 1994, Will has gone one step further in reducing the number of Miller Industries’ distributor locations to approximately 225 worldwide, harnessing the capabilities to export to 67 different countries.
“My father’s belief was that distributors are the key to our success; having the best and most profitable, solid distributors for our products makes Miller Industries successful as a whole”
Will Miller, President, Miller Industries
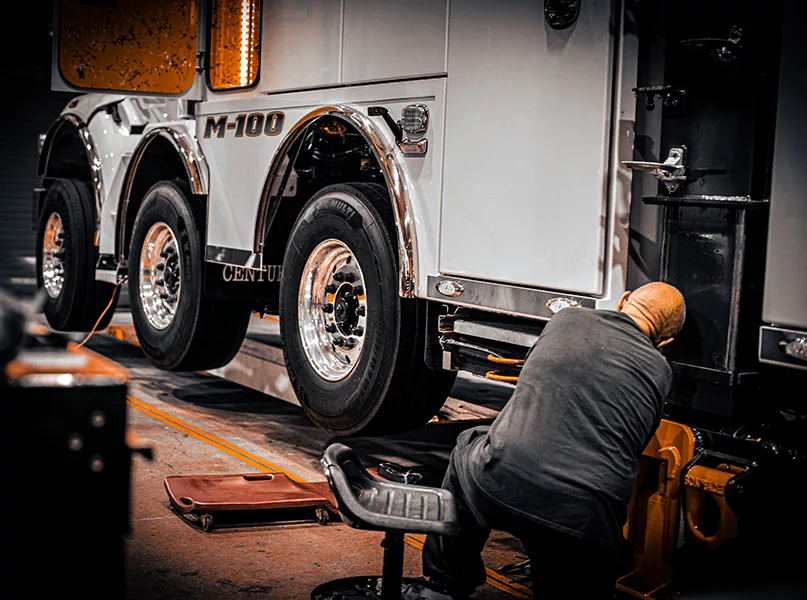
THE BIGGEST AND THE BEST
The company is proud to manufacture the largest portfolio of towing, recovery, and transport vehicles in the world. This includes anything from 8,000 pounds (lbs) of lightduty wreckers up to 100,000 and 200,000 lbs of its largest trucks.
Its diverse network is invaluable for facilitating the company’s enviable global reach. Miller Industries boasts six world-class manufacturing facilities across three countries, with four facilities in the US and one a piece in the UK and France.
The organization is positioned at the forefront of innovation in the towing and recovery industry, thanks to its vast product range and services that consistently break the boundaries of manufacturing.
As part of its portfolio, the company produces light, medium, and heavy-duty wreckers, as well as rotators.
Its light-duty wreckers, known as the Vulcan 812 and the Century Express 312, are utilized throughout the industry for private property, repossession, and cater to commercial towers.
Despite the products’ trusted use throughout the field, Miller Industries is consistently improving its product designs to achieve maximum efficiency for its customers. This can be seen in its light duty lineup where it increased the rear visibility between the boom and the tailboard that facilitates greater hook-up ability, the recently introduced hose tracking system for longer life and easier maintenance, along with giving customers more choices with several hand-held controllers and other options available.
Also notable is the Century 5130, Miller Industries’ best-performing heavy-duty wrecker with 128 inches of underlift reach. This gives users of the wrecker the ability to tow the majority of vehicles without sacrificing the maneuverability of a single axle or tandem axle unit. The product also affords customers a highly advantageous 25-ton recovery boom and 25,000 lbs winches for a vast range of recovery and lifting applications.
Another highly significant component of Miller Industries is its rotator product, Century 1150. Seen as an industry staple, the 50-ton rotator is ideal for daily recovery tasks or more complex needs, with 360-degree continuous boom rotation.
The company is the only manufacturer of recovery equipment capable of meeting tower needs and safety, making it a highly sought-after resource in the towing and recovery sector. The rotator is also ideal for the quick clearance of congested railways, ensuring the swift recovery of vehicles.
Thirdly, Miller Industries is also an industry leader in the production of light, medium, and heavy-duty carriers.
To date, it operates the largest dedicated carrier platform, comprising over 200,000 square feet (sqft), solely committed to building carriers that keep up with the demands of the industry.
One example is the 12 Series LCG™ (low center of gravity) carrier. Through a specialized patented design, it lowers by a much greater degree than conventional carriers used by competitors, whilst also offering greater stability in the transportation of taller loads.
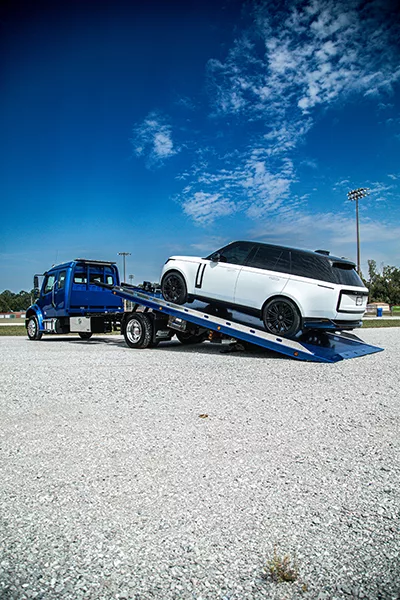
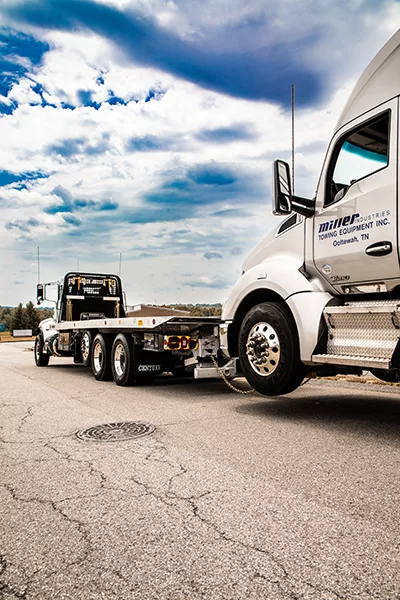
LEADERS IN INDUSTRY INNOVATION
Whilst Miller Industries thrives with the largest and most successful distribution network in North America, what differentiates the company globally is its unmatched product quality, reputable after-sales service, and history of record-breaking vehicles.
The notion of continuous tradition is ingrained in the company, as Miller Industries is the product of a diverse and forward-thinking sector that has cultivated some of the most well-known machinery and vehicles of the modern era, such as the Model T Ford.
Following this, the car manufacturing sector progressed from body-on-frame construction to unibody construction in the 1960s, which can still be seen in many passenger vehicles today.
Also known as chassis frames, body-on-frame construction is used primarily in commercial vehicles, pick-up trucks, and sports utility vehicles (SUVs), whilst most other vehicles are transferred to unibody construction.
Over the years, the company has proactively reacted to changes and innovations in the sector, as it had to alter the way in which it recovers and tows a vehicle in order to stay on top of industry changes and to ensure the safety of products.
For example, Miller Industries navigated the shift in the 1990s from light-duty recovery vehicles and wreckers to car carriers and platforms by building its first dedicated carrier manufacturing facility in 1994 in Hermitage, Pennsylvania, making multiple additions to the factory over time.
Furthermore, there was a noticeable shift in light-duty wreckers from conventional wreckers of the early 2000s to auto loads – low profile crossbars that go under a vehicle to grab it by its front tires rather than using a chassis frame.
“These wreckers have hydraulic claws that reach around the tires so you can pick up half the vehicle singularly by the front or back wheels, showing a serious evolution,” Will explains.
Regarding heavy-duty products, large over-road-chassis have gotten lower to the ground and more aerodynamic as the industry has progressed, resulting in better fuel economy. Consequently, the company reduced the height of the crossbar device that comes into contact with the vehicle.
“We’ve had to make it increasingly thinner whilst retaining its strength. The crossbar is now down to five inches in height so they can fit underneath the bumpers of commercial vehicles easily.
“This also means that we can still tow vehicles without damaging their dynamic fairings and underbody,” he adds.
Another aspect Miller Industries pays close attention to is weight. It wants to ensure that its vehicles comply with all road safety standards and do not exceed the maximum weight allowance of public roads, whilst still being strong enough to efficiently tow the desired vehicle.
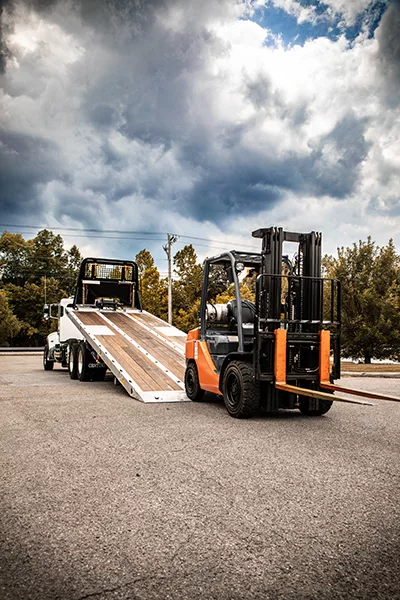
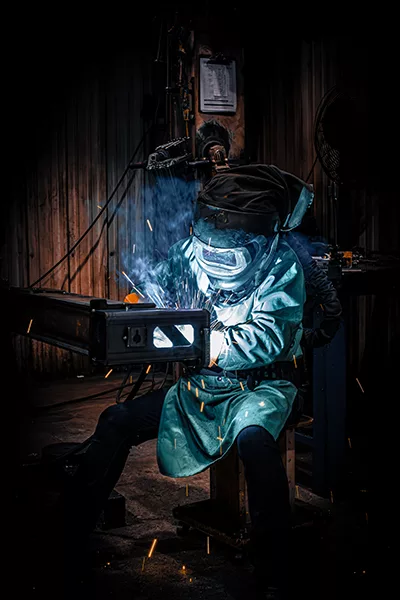
ACHIEVING VERTICAL INTEGRATION
With continuous improvement as a hallmark of the business, the company has invested over $100 million in its manufacturing facilities globally in just over a decade, particularly in its paint capabilities and robotics, as well as developing a dedicated R&D center.
Miller Industries specifically focused on vertical integration during the COVID-19 pandemic in 2020, at a time when a lot of its competitors were slowing down production and letting staff go.
During this period, the company invested in a state-of-the-art fabrication equipment facility to begin the production of its own steel parts, growing its in-house capabilities.
Meanwhile, staff whose work had stagnated due to the decreased demand were given the opportunity to go to training centers to learn how to operate computer numerical control (CNC) machines, as well as control lasers, press brakes, plasmas, and lay mills. This contributed to the wider goal of having a functioning workforce that can efficiently operate new, highly automated, world-class fabrication equipment.
The company’s vertical integration process also included the introduction of an enterprise resource planning (ERP) system in 2019, which allowed Miller Industries to succinctly run all its worldwide facilities, streamlining operations in manufacturing, human resources (HR), accounting, and engineering.
The ERP system comprises a cloud-based piece of software called CloudSuite Automotive, created by Infor, which enabled the company to handle over a billion dollars of revenue in preparation for 2024.
“As a manufacturing organization, a solid software system allows us to expand organically and harness additional acquisitions and the future growth of Miller Industries,” Will highlights.
The company’s second phase of vertical integration in Q2 2023 witnessed the acquisition of Southern Hydraulics Cylinder (SHC). The entity had previously been a supplier; therefore, the acquisition was a natural step to progress Miller Industries into the wider manufacturing space, having more control over certain supply chain issues.
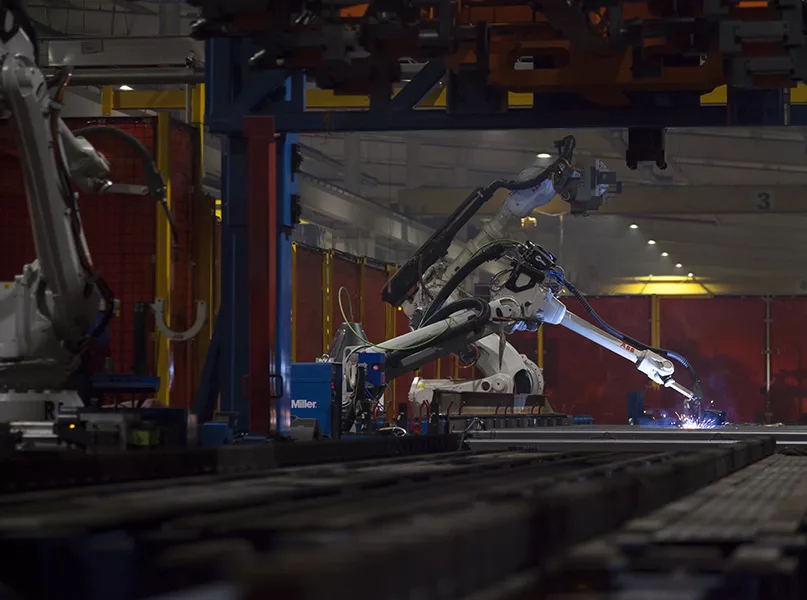
DIVERSE, FAIR, AND ENGAGED
At the heart of the company lies Miller Industries’ staff base, who are continuously valued across the organization. Considered a profit-sharing company, it has a strict bonus structure applicable to all employees so that each team member can take home a percentage of net profit.
Alongside company-wide financial incentivization, Miller Industries also invests in human capital and the health and safety of its employees. These standards include climate-controlled facilities, LED lighting, and overall enhancement in the work environment.
As of last year, the company also introduced an employee family scholarship fund, into which each of the executives commits to putting $5,000 per year, a figure that the wider company then matches.
This generosity is used to facilitate 14 higher education scholarships for either the children or grandchildren of employees.
This is compounded further by the Frontline Leadership Academy, which provides tuition reimbursement to further the education of its employees. Additionally, Miller Industries also possesses an in-house welding academy where high school students and former military personnel can become skilled welders to further the productivity of its facilities.
In accordance with its commitment to employee well-being and personal development, the business strives to create an environment that is inclusive, diverse, fair, and engaged.
To meet these high standards, the company has implemented a specific diversity, equality, and inclusion (DEI) program that is consistently monitored to see how it could be improved. For example, in 2022, Miller Industries introduced an anti-harassment and anti-discrimination policy as part of the program.
On top of this, the company also regularly monitors DEI metrics to develop its minority representation, as well as having a proactive hiring process that welcomes veterans, women, and underrepresented minority groups.
BREAKING BARRIERS
At the forefront of the towing and recovery sector’s innovation, Miller Industries is immensely proud to have developed and created the Century M100 100-ton rotator. The product came into ideation in 2017 after the company identified a greater market demand for a higher capacity product.
MILLER INDUSTRIES PARTNER
