Revolutionizing rail travel, Stadler US is making its mark with its state-of-the-art facility, which manufactures cutting-edge trains that are not only tailored to meet the unique needs of customers but also set new standards in the industry.
THE PERFECT PRODUCTION PLATFORM
Since the 1820s, railroads have played a pivotal role in US transportation.
Initially, horses and steam engines pulled rudimentary wooden freight cars, but as the industry evolved, the US soon began developing its own rail manufacturing capability as early as the 1830s.
During the Industrial Revolution, railroads advanced significantly, becoming a critical mode of transportation for raw materials over long distances. Since then, trains have undergone major improvements, a testament to the innovation and growth of the rail travel industry.
Not only did this progress shape the nation’s infrastructure and economy, but it also laid the foundations for companies like Stadler US to thrive.
Stadler US is the stateside division of Swiss manufacturer, Stadler Rail, whose rich history dates back to 1942 when Ernst Stadler founded an engineering office in Zurich.
Three years later, Stadler Rail began producing battery and diesel-powered locomotives, with its first passenger vehicles rolling off the production line in 1984. This history of innovation and expertise has been a cornerstone of the company’s success and earned it a reputation for reliability and trust in the rail travel industry.
In 1989, Stadler Rail made a groundbreaking contribution with the introduction of the first modular vehicle. This innovation paved the way for successful business development and solidified the company’s position as the world’s leading manufacturer in the rack and pinion sector.
These lightweight vehicles, equipped with various rack and pinion systems as well as track gauges, are designed to handle extreme landscapes and gradients, showcasing Stadler Rail’s long-standing leadership in the industry.
Today, Stadler US has a varied product range of rail cars and rolling stock for the North American market, spanning from trams to high-speed trains.
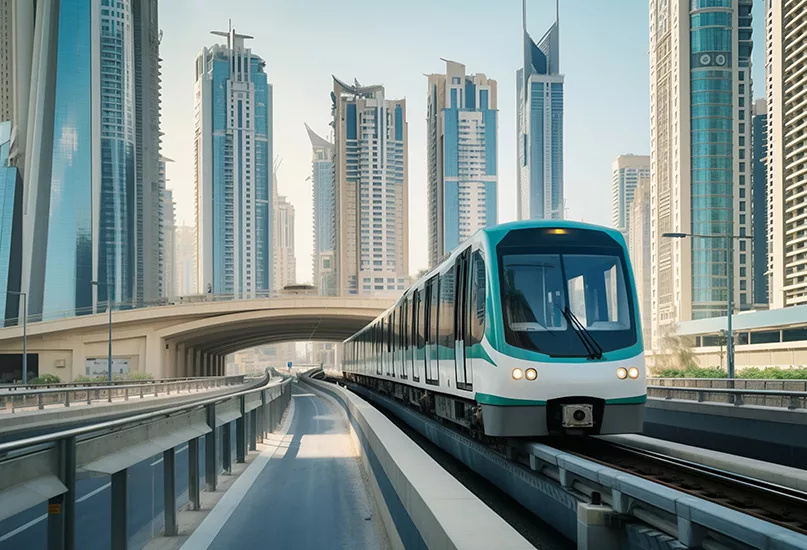
SUSTAINABLE BY RAIL
Although the company has been operating in the country since 2002, it wasn’t until 2019 that Stadler US opened its first production site in Salt Lake City, Utah.
The facility imports car shells and bodies from Europe, but Stadler US plans to change this to reduce its carbon footprint.
In 2022, the company also signed a Memorandum of Understanding (MoU) with the California State Transportation Agency (CalSTA) and the California Department of Transportation (Caltrans) for the design and delivery of four zero-emission trains, with the option to purchase up to 25 units.
FLIRT has been successfully operating in extreme climates worldwide, from Africa to the Arctic Circle. As part of the company’s range of alternative solutions, the FLIRT H2 model utilizes hydrogen fuel cells as its energy source.
The train operates entirely on electricity and stores kinetic energy in batteries under braking. The electricity generated is then used to power the train, charge the lithium-ion traction batteries, and feed the onboard heating, ventilation, and air conditioning (HVAC) system. The propulsion system, meanwhile, allows FLIRT H2 to operate throughout the day without refueling.
Stadler US delivered the first hydrogen-powered train for passenger rail transport in 2019, selling its first FLIRT H2 vehicle in the country. The lightweight aluminum single-decker model can be arranged in two to four-car compositions.
This year, Stadler US proudly announced that the FLIRT H2 was entered into the Guinness World Records database for the longest distance achieved by a pilot hydrogen fuel cell electric multiple-unit passenger train without refueling or recharging – 1,741.7 miles.
The company’s innovative strength and technological prowess in sustainable rail transport have been highlighted by this impressive achievement.
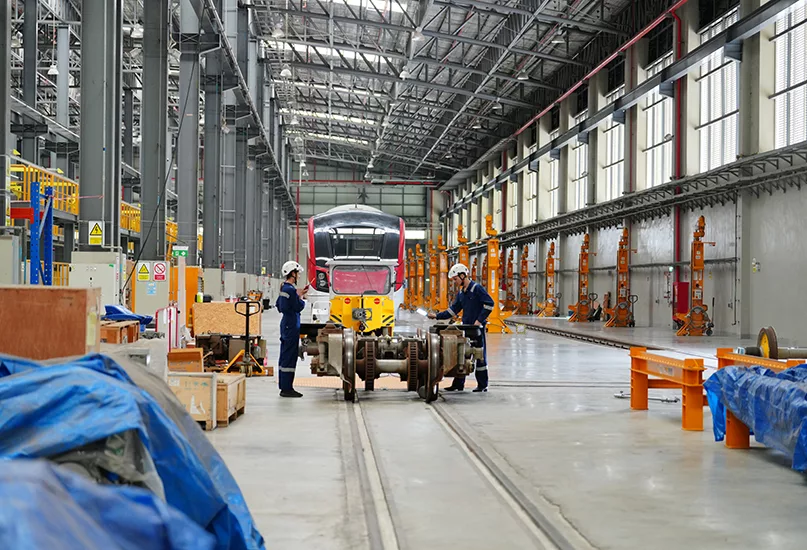
TAILOR-MADE TRAINS
Stadler US is happy to create custom vehicles to suit each customer.
After starting with the production of single vehicles and small-batch series, the company now offers many years of experience and engineering expertise to meet specific needs, guaranteeing flexibility and quality.
Rail operators benefit from Stadler US’ personalized approach, allowing for tailor-made locomotives to meet special requirements in construction, shunting, and journeys with combined gear wheels and adhesion.
Alongside trains, Stadler US offers customized signaling and digital solutions and services to ensure efficient and sustainable rail operations. It also provides continuous customer care beyond train delivery, ensuring reliable and safe rail operations.
Stadler US trains are produced in small series and optimized for individualization and quality, in contrast to the model series of tailor-made multiple units. The company offers custom-made carriages for driving trailers, passenger cars, panoramic carriages, and sleepers with a wide range of interior design, HVAC, and technology options.
Furthermore, its trains are cost-effective and cutting-edge, providing passengers with maximum comfort.
FULL STEAM AHEAD
In 2019, Stadler US was also contracted by the Dallas Area Rapid Transport (DART) to build eight FLIRT trains and design the equipment maintenance facility (EMF) for the Cotton Belt Regional Rail Project.
In the same year, the Metropolitan Atlanta Rapid Transit Authority (MARTA) awarded Stadler US a contract worth over $600 million to build 127 metro trains for the Atlanta area.
The contract specified that the new trains must be based on the previous models and required the integration of modern technology into the old specifications.
Stadler US has implemented a Youth Apprenticeship Program inspired by the Swiss model to handle the high volume of contracts it receives.
This program is designed to ensure that the company has the necessary talent to complete the orders. In the first year, students can choose between the Automatic Technician (electrical) and Production Technician (mechanical) tracks.
In the second year of their apprenticeship, trainees attend courses at Salt Lake Community College, receive supplementary training from Stadler US, and are integrated into regular production.
In the final year, advanced lectures are conducted at the college, whilst more skilled, practical training continues at the company. To graduate from the program, apprentices must successfully complete final testing and a final project.
The purpose of the intensive training is to ensure Stadler US maintains the high standards of the long and illustrious history of Stadler Rail.
STADLER US PARTNERS
